كيمياء المصلبات القائمة على الأمين في أنظمة راتنجات الإيبوكسي
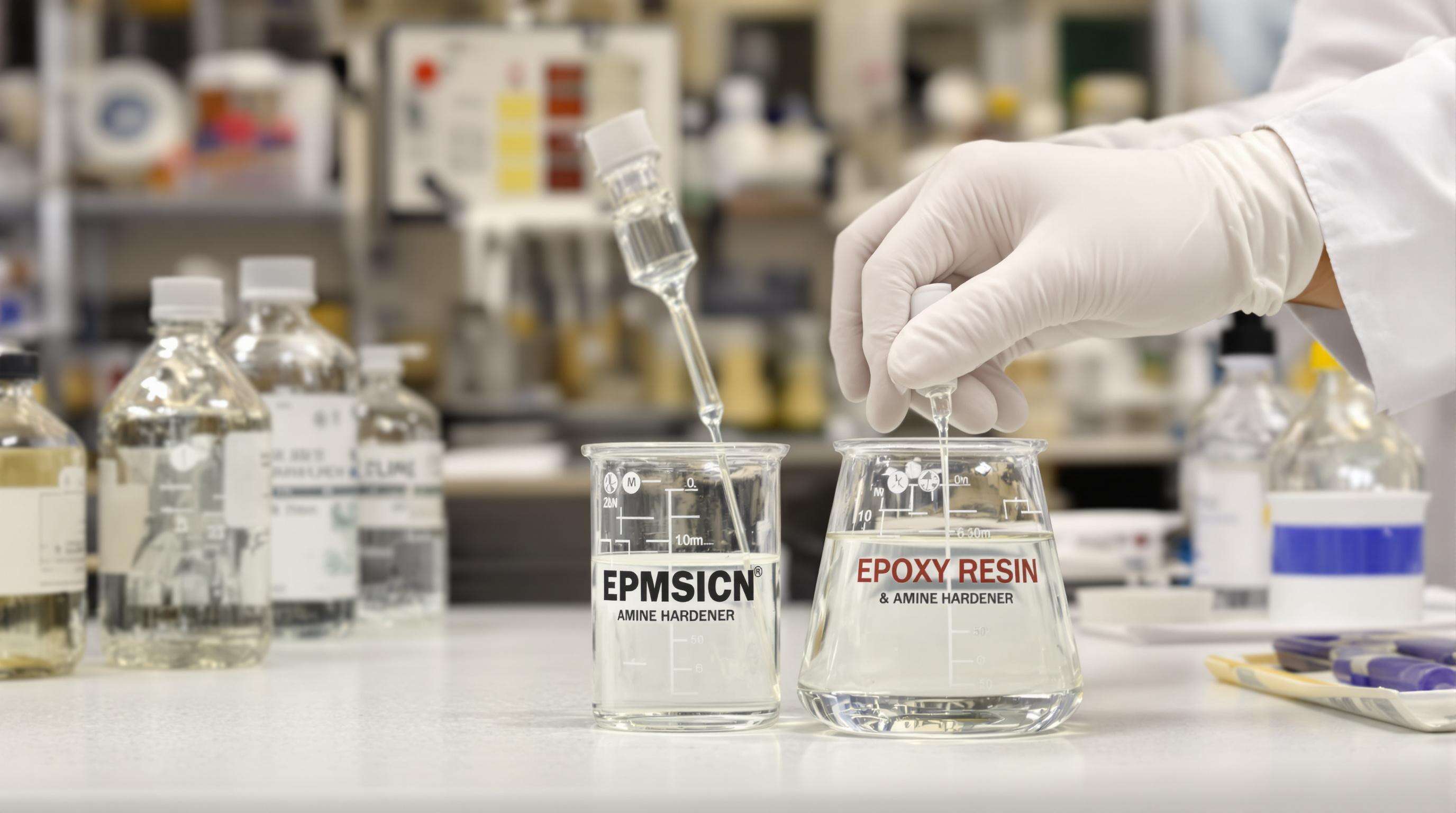
يتم إعداد راتنجات الإيبوكسي غالبًا باستخدام متصلدات الأمين بسبب تفاعلها الواسع وقدرتها على تحقيق توازن في القوة. تقوم هذه العوامل المتشابكة بإحداث تشابك عبر إضافة نووية، حيث تتفاعل مجموعات الأمين (-NH) مع حلقات الإيبوكسي لتشكيل شبكة حرارية ثلاثية الأبعاد. تختلف بيانات التصلب بشكل واسع - فأنواع الشمع تصلب خلال 3 ساعات إلى 24 ساعة عند درجة حرارة 25°م (68°ف)، وأنواع العطرية تحتاج إلى حرارة أعلى لتحقيق أفضل تبلمر.
ميكانيكيات التفاعل المؤثرة على سرعة التصلب
تخضع الأمينات الأولية والثانوية لتفاعل مباشر مع مجموعات الإيبوكسي من خلال التكاثف التدريجي للبوليمر، بينما تعمل الأمينات الثلاثية على تحفيز آلية النمو السلسلي الأنيونية. كما أن المجموعات الألكيلية في الأمينات الأليفاتية لها تأثير إعطاء إلكترونيات ما يؤدي إلى تسريع معدلات التصلب بنسبة 30–40% مقارنةً بالنظم العطرية. هذه التفاعلية تسمح بتعديل واسع لنطاق عمر الجلوتينغ - من لاصقات تتطلب 15 دقيقة إلى طلاءات صناعية تحتاج إلى 8 ساعات.
مزايا الاستقرار الحراري للتطبيقات ذات الحرارة العالية
تُظهر الإيبوكسيات المعالجة بالأمينات درجات تحلل تتجاوز 180°م (356°ف)، مما يجعلها مناسبةً للمركبات الفضائية ومكونات السيارات الموجودة تحت الغطاء. توفر الأمينات الدورية الأليفاتية استقرارًا حراريًا محسنًا من خلال هياكل حلقية صلبة، في حين تتيح الإضافات مثل البورون أو الفوسفور الحصول على تصنيف UL 94 V-0 لمثبطات اللهب في عوازل الطاقة الكهربائية.
قيود الحساسية للماء في البيئات الرطبة
تمتص معالجات الأمين الهيدروفيلية الرطوبة المحيطة عند رطوبة نسبية تزيد عن 60%، مما يؤدي إلى اكتمال غير كلي للعمران وتقليل في قوة الشد بنسبة 15-20%. يواجه المصنعون هذه المشكلة باستخدام مواد معدّلة هيدروفوبية مثل الكاردينول أو السيلوكسانات، مما يقلل من امتصاص الماء بنسبة 50% في البيئات البحرية.
تعديلات اللزوجة المقارنة أثناء التطبيق
عادةً ما تكون للمعالِجات الأمينية غير المعدّلة لزوجة تتراوح بين 200–500 سنتي بويز. تُقلل المواد المخففة التفاعلية مثل الإيثرات الغلايسيدية من اللزوجة لتصل إلى 80–120 سنتي بويز، مما يسمح بتركيب طبقات الألياف المدعمة دون حدوث تشوهات. تُحتفظ بالبولي أمينات ذات الوزن الجزيئي العالي (1000–2000 سنتي بويز) لمجالات استخدامها في ألعواصم المُعبئة للفراغات.
معالجات أنهيدريد للأ,epoxy resins المقاومة للحرارة
توفر معالجات الأنهيدريد استقرارًا حراريًا استثنائيًا، حيث تتحمل التعرض المستمر لدرجات حرارة تتجاوز 150 درجة مئوية. تقاوم هياكلها العطرية التدهور الحراري، مما يجعلها خيارًا مثاليًا للتطبيقات الجوية والسياراتية.
تفاعلات طرد الحرارة المؤجلة التي تقلل من الإجهادات الداخلية
تُظهر متبلمرات الإيبوكسي-أنهيدريد تأخيرًا في قمم التفاعل الحراري، مما يقلل من التدرجات الحرارية وإجهادات الانكماش في الصب السميك. إن تمديد زمن التجمد (~90-120 دقيقة) يقلل التشوهات في أدوات المركبات بنسبة 40-60%.
الخصائص العازلة ضرورية لتطبيقات الغلاف الإلكتروني
توفر صمغ الإيبوكسي المعالج بـ أنهيدريد مقاومة عازلة ممتازة (>20 كيلو فولت/ملم) مع تلوث أيوني منخفض جدًا (<10 جزء في المليون)، وهو ما يتوافق مع معايير IPC-CC-830B الخاصة بالعوازل في وحدات الطاقة والمتحولات. تقلل هذه التركيبات من التفريغ الجزئي بنسبة 30% مقارنةً بالراتنجات القياسية في تطبيقات خزانات التوزيع.
مواد التصلب البولي أميدية تعزز المرونة في صمغ الإيبوكسي اللاصق
تعطي مواد التصلب البولي أميدية أديبات لاصقة مرنة يمكنها تحمل الاهتزاز والدورات الحرارية. إن سلاسل الكربون الطويلة فيها تعزز المطيلية دون التأثير على قوة التماسك - حيث تحتفظ صمغ الإيبوكسي المعالج ببولي أميد بـ 85% من قوته اللاصقة بعد 1000 دورة صدمة حرارية (-40°م إلى 100°م).
أهم فوائد المرونة
- يتكيف مع اختلافات التمدد الحراري
- يمتص الاهتزازات الميكانيكية
- يحافظ على سلامة الوصل على الأسطح المرنة
- يقلل من تشققات دقيقة أثناء التشويه
مواد كيميائية متخصصة من نوع فينالкамين تؤثر على مقاومة المواد الكيميائية
توفر معالجات الفينالكامين مقاومة كيميائية استثنائية، حيث تتحمل أكثر من 500 ساعة من الغمر في المذيبات القاسية وفي درجات حرارة متطرفة من الأس الهيدروجيني. كما أن تسامحها مع الرطوبة يقلل من العيوب السطحية مثل تشقق الأمين، مما يقلل معدلات الرفض بنسبة 40٪ في التطبيقات البحرية.
تعمل هذه التركيبات على التصلب بشكل فعال عند درجات حرارة منخفضة تصل إلى 0°م، مما يجعلها مثالية للاستخدام في الظروف الباردة، بينما تدعم قوتها العازلة التغليف الكهربائي. تمتد دورات الصيانة في المصانع الكيميائية لمدة أطول تتراوح بين مرتين إلى ثلاث مرات باستخدام أنظمة الفينالكامين.
اختلافات الخواص الحرارية الميكانيكية حسب كيمياء المُعالج
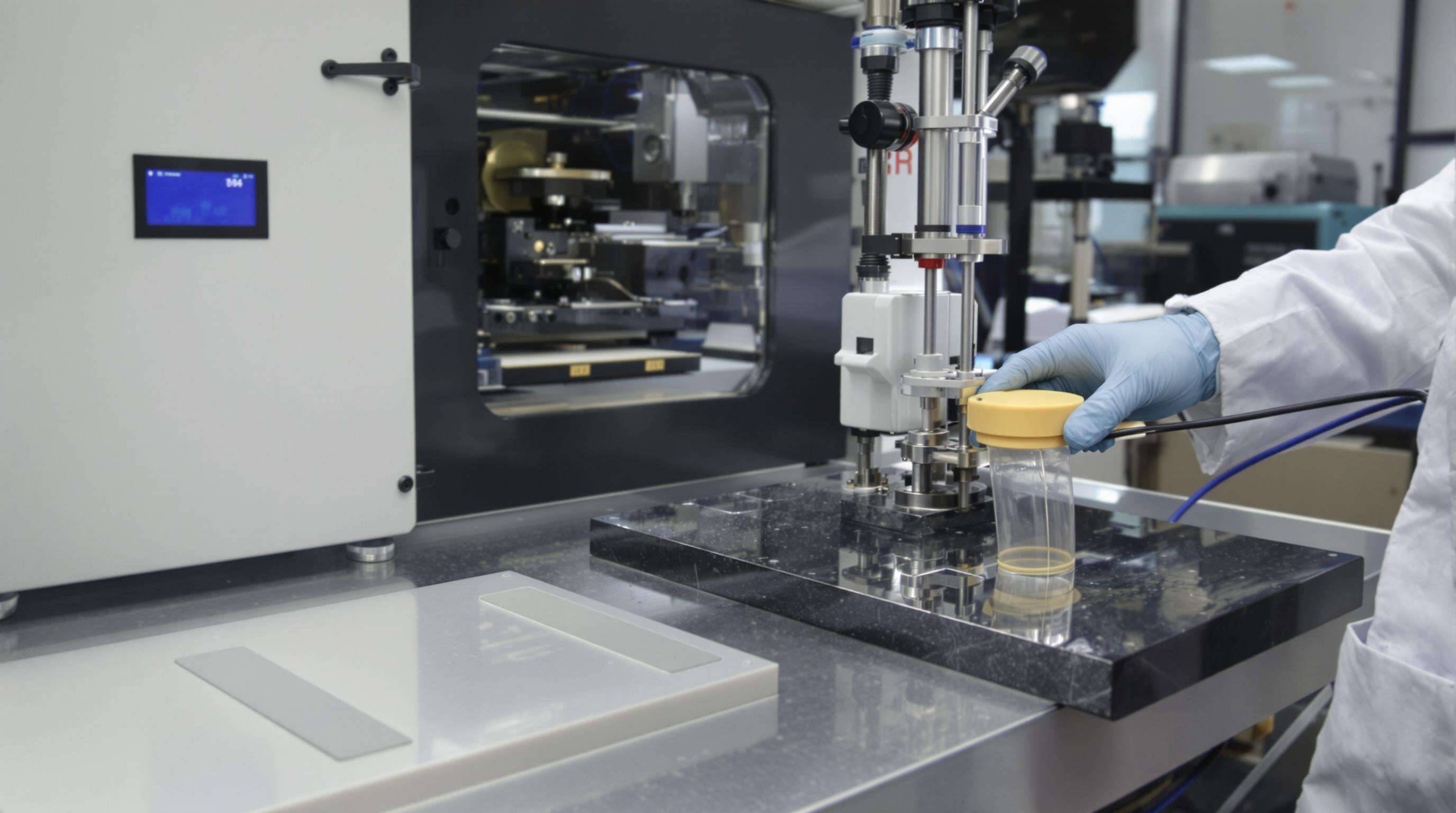
تغيرات درجة حرارة الانتقال الزجاجي عبر التركيبات المختلفة
يزيد مُعالجا الأمين المُعدّل من درجة حرارة الانتقال الزجاجي (T g ) بنسبة 38% من خلال دمج مجموعات عطرية صلبة. مع كل زيادة بنسبة 10% في كثافة التشابك، ترتفع درجة الحرارة g ترتفع حوالي 15°م في الأنظمة المحسنة حرارياً.
إدارة معامل التمدد الحراري (CTE) لضمان توافقية الركيزة
تقلل مواد التصلب البطيئة من أنهيدريدات معامل التمدد الحراري (CTE) بنسبة 22%، وتحقق قيماً ضمن نطاق 1.5 جزء في المليون/°م من ركائز الألومنيوم الخاصة بالالتصاق في صناعة الطيران.
التعويض بين المتانة والمرونة في الأنظمة المعدلة
تزيد الأنظمة المُعدّلة بولي أميد من مقاومة الكسر بنسبة 47٪ ولكنها تقلل المرونة بنسبة 12-18٪. توازن معالجات الهجين بين هذه الخواص، حيث تحقق مقاومة تمزق تبلغ 30 كيلو نيوتن/متر مع الحفاظ على 85٪ من الأداء الانثنائي.
استراتيجيات تحسين وقت التصلب لمُعالجي راتنجات الإيبوكسي
يُقلل رفع درجات الحرارة إلى 120 درجة مئوية من فترات المعالجة بنسبة 85-92% مقارنةً بالتصلب في درجة حرارة الغرفة. تُتيح مُصلِّبات الأمين المُعدّلة خاصية "المعالجة عند الطلب" مع معالجة في أقل من 60 ثانية، بينما تضمن أنظمة الحقن ثنائية المكونات انحرافًا في نسبة الخلط بنسبة أقل من 2%. تُوفر تركيبات عمر العبوة المُمتد ثباتًا على الرف لأكثر من 6 أشهر مع معالجة كاملة في أقل من 5 دقائق بعد الاستخدام.
يركز الاختيار القائم على السوق على الاستدامة والأداء المخصص للتطبيق، مع ابتكارات تستهدف بطاريات السيارات الكهربائية وشفرات توربينات الرياح والطلاءات المقاومة للتآكل.
الأسئلة الشائعة (FAQ)
ما هي فوائد استخدام المصلبات الأمينية في راتنجات الايبوكسي؟
تُوفر المُصلِّبات الأمينية نطاقًا واسعًا من التفاعلية والقوة المتوازنة. كما تُتيح أوقات تصلب سريعة واستقرارًا حراريًا مُحسَّنًا، خاصةً للتطبيقات عالية الحرارة.
لماذا يتم استخدام مقويات الأنهيدريد للراتنجات الإيبوكسي المقاومة للحرارة؟
توفر مواد التصلب الأنيهيدرية استقرارًا حراريًا استثنائيًا، وتحمّل التعرّض الطويل لدرجات الحرارة المرتفعة، وتتميز بخصائص عازلة ممتازة، مما يجعلها مثالية للتطبيقات الجوية والautomotive.
كيف تحسّن مواد التصلب البولي أميدية المرونة في اللواصق الإيبوكسية؟
تُنشئ مواد التصلب البولي أميدية لواصق مرنة قادرة على تحمل الاهتزاز والدورات الحرارية. وتوفر سلاسل الكربون الطويلة التي تتمتع بمرونة متزايدة دون التأثير على قوة التماسك.
ما الفوائد التي توفرها مواد التصلب المتخصصة الفينالكامينية؟
توفر مواد التصلب الفينالكامينية مقاومة كيميائية استثنائية، وتسامحًا مع الرطوبة، وتتصلب بشكل فعّال عند درجات الحرارة المنخفضة، مما يمدّد دورات الصيانة ويقلل من العيوب السطحية.
كيف يمكن تحسين أوقات المعالجة لمصلبات الراتنج الإيبوكسي؟
يمكن تحسين أوقات التصلب عن طريق رفع درجات الحرارة واستخدام مواد تصلب أمينية معدلة بوظائف "التصلب عند الطلب". تُقلل هذه الممارسات من فترات التصلب بشكل كبير مع الحفاظ على الأداء.
جدول المحتويات
- كيمياء المصلبات القائمة على الأمين في أنظمة راتنجات الإيبوكسي
- معالجات أنهيدريد للأ,epoxy resins المقاومة للحرارة
- مواد التصلب البولي أميدية تعزز المرونة في صمغ الإيبوكسي اللاصق
- مواد كيميائية متخصصة من نوع فينالкамين تؤثر على مقاومة المواد الكيميائية
- اختلافات الخواص الحرارية الميكانيكية حسب كيمياء المُعالج
- استراتيجيات تحسين وقت التصلب لمُعالجي راتنجات الإيبوكسي
-
الأسئلة الشائعة (FAQ)
- ما هي فوائد استخدام المصلبات الأمينية في راتنجات الايبوكسي؟
- لماذا يتم استخدام مقويات الأنهيدريد للراتنجات الإيبوكسي المقاومة للحرارة؟
- كيف تحسّن مواد التصلب البولي أميدية المرونة في اللواصق الإيبوكسية؟
- ما الفوائد التي توفرها مواد التصلب المتخصصة الفينالكامينية؟
- كيف يمكن تحسين أوقات المعالجة لمصلبات الراتنج الإيبوكسي؟